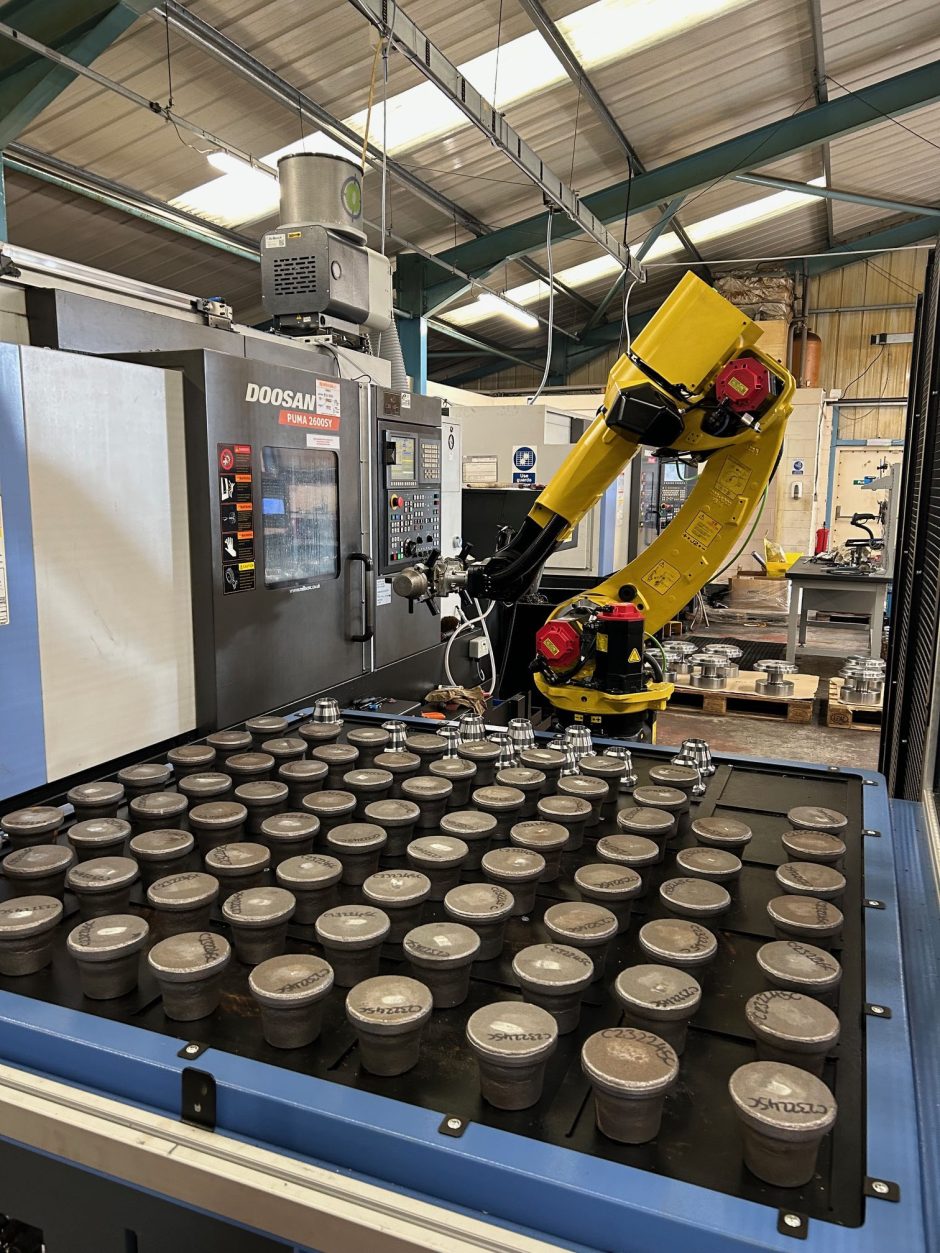
Ayrshire Precision transforms its small turned part processing operations by investing in two SYNERGi automation systems and integrating them with two, existing Doosan Puma Y-axis, sub-spindle lathes.
The creation of two, self-contained automated manufacturing cells has helped the company significantly increase its productivity and process efficiencies by embracing unmanned and lights-out production.
The investment in sophisticated automation technology from Mills CNC is delivering real, tangible and sustainable benefits that include a) eliminating production bottlenecks and pinch points, b) reducing part cycle times and, as a consequence, customer lead times, and c) being able to realise the full machining capacity potential of two, previously under-utilised, lathes.
Mills CNC, the exclusive distributor of DN Solutions’ and Zayer machine tools in the UK and Ireland, and a leading supplier of its SYNERGi automated manufacturing cells to component manufacturers, has recently supplied Ayrshire Precision, a leading precision subcontract specialist based in Ayrshire, with two new SYNERGi systems.
The systems, both derivations and highly-customised versions of Mills’ standard SYNERGi ‘SPRINT’ solutions, were installed at Ayrshire Precision’s 14,000sq. ft. in 2023 – the first being retrofitted to a Puma 2600SY lathe in March, and the second, also retrofitted, to a Puma 2100SY in September.
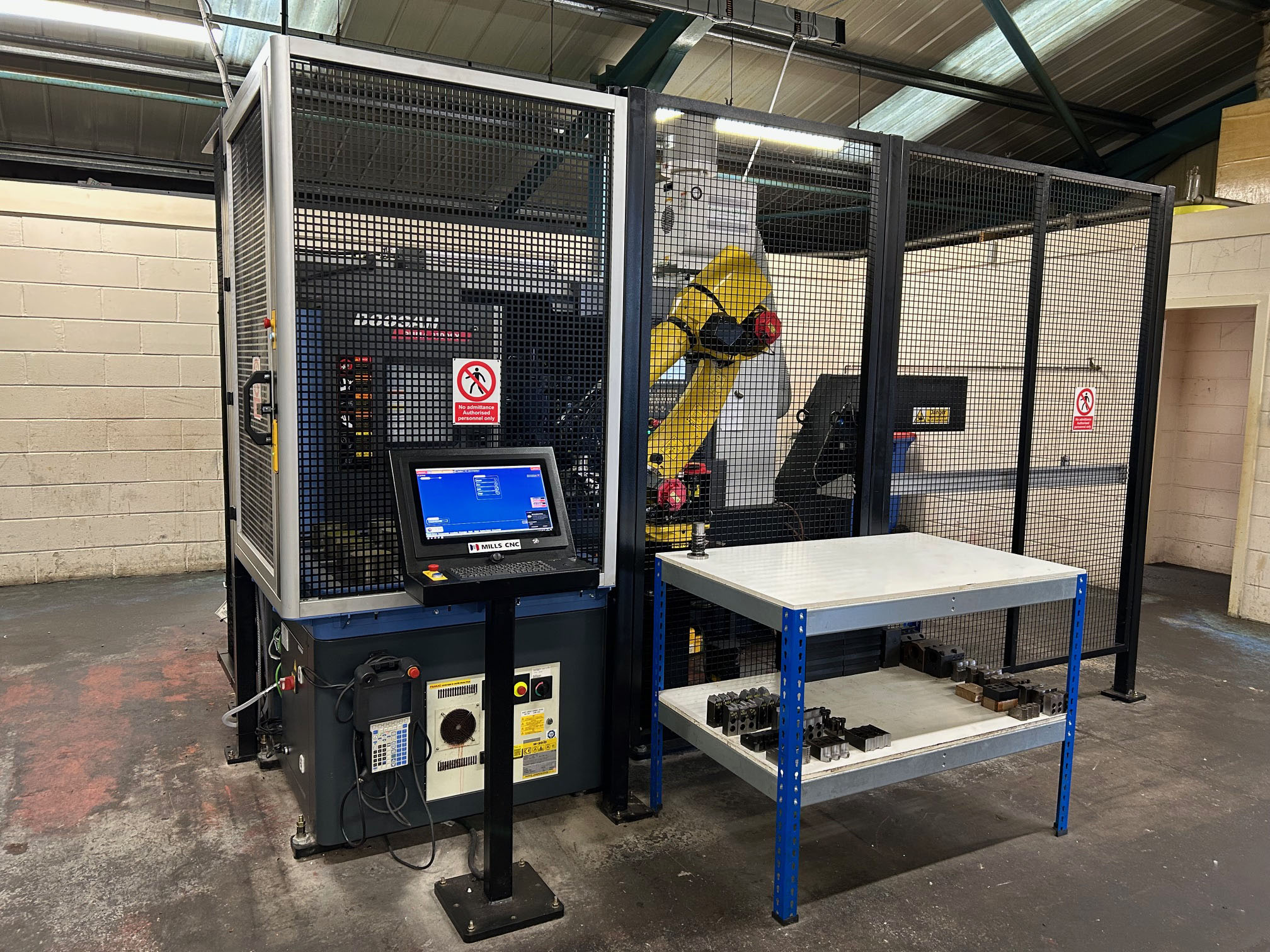
SYNERGi Sprint – a closer look
SYNERGi Sprint automation systems are compact, flexible and cost-effective.
They can be integrated with DN Solutions’ lathes, machining centres and mill-turn machines by Mills’ dedicated automation experts to create high-productivity automated manufacturing cells.
The basic elements of a SYNERGi Sprint system comprise the following:
- An industrial Fanuc robot with varying payloads and reaches, in large part determined by the weight of component being machined: Typically a robot with a 20kg to 35kg payload is supplied
- 2- or 3-jaw pneumatic grippers (end effectors)
- A 900mm x 900mm part loading/unloading grid plate, although customised sizes can be accommodated to handle larger workpieces and batch volumes
- Industrial safety guarding positioned around the system
- SYNERGi software and a 17” touchscreen HMI for programming and monitoring
Mills can also supply customers with multi-socket inserts to optimise each system’s capacity. These are sheet metal fabrications that customers can also choose to manufacture for themselves.
Ayrshire Precision background
Ayrshire Precision, established in 1969, is an innovative precision subcontract specialist machining high-quality components to a range of customers in the oil and gas, subsea, renewables, power generation and aerospace sectors.
The company has a well-resourced machine shop and, as part of its ongoing continuous improvement programme, regularly invests in its people, its plant and equipment, and in its processes and systems. Over the years, the company has invested regularly in new machine tools as a route to increasing its in-house machining capacity and capabilities; a high percentage of which have been Doosan machines from Mills CNC.
Relationship with Mills CNC
Since 2012 Ayrshire Precision has invested in a range of Doosan machines, from two-axis and multi-tasking lathes through to large-capacity, heavy-duty vertical machining centres and horizontal borers, to machine complex, high-precision components made from steels, stainless, duplex, Inconel and other difficult-to-machine materials.
“We rely on machine tools from Mills.
“They are powerful, fast and accurate and enable us to meet the highly-regulated, tight-tied up tolerances and exacting surface finishes that characterise a majority of the components we machine.”
Chris Hepburn, Managing Director at Ayrshire Precision
In addition to the actual technologies Mills supplies, Ayrshire Precision also holds Mills’ pre- and after-sales services in high regard and, in addition to taking advantage of its CNC training courses, also uses Mills for CNC machine servicing etc.
Automation decision
Ayrshire Precision’s decision to invest in automation was made for a number of reasons.
The volatility of the markets served by the company and, as a consequence, fluctuating customer demand for the company’s machining services, combined with a difficulty in recruiting and retaining skilled labour, all contributed to Ayrshire Precision’s decision to ‘think outside the box’, and begin its automation journey.
“It’s either feast or famine in the markets where we operate.
“We can either be very busy or, due in large part to external macro-economic factors that impact on our customers’ business, can experience order cancellations and/or postponements that make it difficult to match our production capabilities and resources with changing customer requirements.”
Chris Hepburn, Managing Director at Ayrshire Precision
Rather than be at the mercy of market forces, and to protect the long-term viability and profitability of the company, Ayrshire Precision made the decision back in 2020 to ‘take the bull by the horns’ and explore new ways to improve its flexibility, performance and competitiveness.
The company’s focus was, initially, on its small part turning operation which, at that time, comprised two Puma lathes, running over two shifts, and operated by four members of staff.
To increase the productivity of its Puma lathes the company had previously looked at integrating a bar feeder to each machine. However, the diameters of the drop forged parts being machined, the batch sizes required and the limited (diameter) capacity of the bar feeders themselves, precluded this approach.
This led the company to investigate alternative robot part loading options. And then the pandemic hit.
“Our plans were put on hold to some extent by the pandemic, but the hiatus gave us more time to do our homework and research the market thoroughly to identify the ‘best fit’ automation system for our needs.”
Chris Hepburn, Managing Director at Ayrshire Precision
Ayrshire Precision discussed its requirements with a number of automation system suppliers with the main focus being on the proposed system’s configuration, availability and cost.
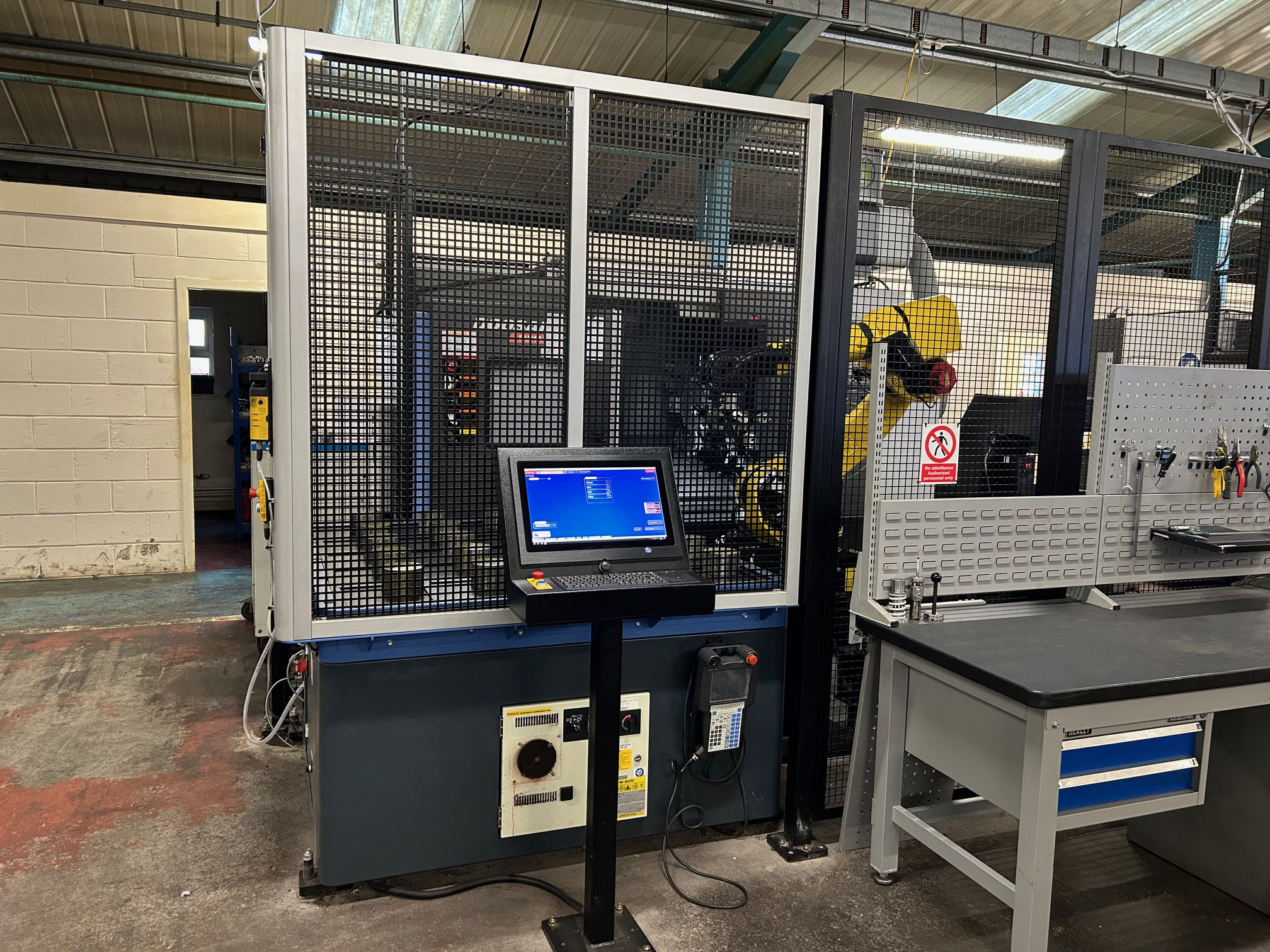
Selecting an automation supplier
As part of its decision-making process, Ayrshire Precision visited Mills CNC – a company that had previously supplied it with eight new (Doosan) machines in the past.
From discussing its plans further with Mills’ automation application specialists and, after seeing a couple of different SYNERGi systems in action at Mills’ Technology Campus facility in Leamington, it was confirmed that two, separate SYNERGi Sprint systems would better meet Ayrshire Precision’s manufacturing requirements.
“We liked the design and build of the SYNERGi Sprint system. It was simple and straightforward.
“We asked Mills to put forward their plans and proposals for two SYNERGi Sprint cells – one incorporating our existing Puma 2600SY for larger parts, and the second incorporating our Puma 2100SY for smaller components.”
Chris Hepburn, Managing Director at Ayrshire Precision
Through the planning process it became clear that, whilst the standard SYNERGi Sprint system would suffice for the Puma 2100SY cell, some customisation would be required for the larger Puma 2600SY cell.
This customisation ultimately resulted in the incorporation of a larger industrial robot with a longer reach radius and a higher payload capacity (35kg), and a bigger table (1200mm x 1200mm) to enable larger batch sizes to be processed.
“Mills’ approach was responsive and helpful. They worked with us to tailor make the SYNERGI Sprint systems and offered lots of useful advice that would stand us in good stead once the systems were delivered and installed.
“We placed the business with Mills, not just because of their technical and automation expertise, but also because the two Puma lathes had originally been supplied by them and they knew the machines inside out.
“We also thought that dealing with one supplier for our machine tool and automation system requirements (i.e., one point of contact) would be easier and would simplify communications, servicing, training etc.”
Chris Hepburn, Managing Director at Ayrshire Precision
SYNERGi (Sprint) Cell 1
Ayrshire Precision’s first manufacturing cell was installed in March 2023.
The cell comprises a Puma 2600SY multi-tasking lathe, a Fanuc 35kg industrial robot with dual Schunk 3-jaw grippers, a 1200mm x 1200mm table with 1 x multi-socket insert with 25 separate pockets – each accommodating 4 components.
Other elements include requisite Renishaw probing systems, safety caging that goes around the cell and the system’s HMI control driven by Mills’ proprietary SYNERGi software.
The whole installation, which occurred on site at Ayrshire Precision’s facility, took approximately 4 weeks to complete and included the building of the cell, robot teaching and operator training.
The cell, when using the 25 pocket insert, enables 100 parts to be machined unattended – a majority of which are processed overnight.
With individual part cycle times being approximately 10 minutes, Ayrshire Precision is now benefiting from up to an additional 16 hours of unmanned operation of its Puma 2600SY lathe.
Since installation, the company has manufactured different sheet metal pocket inserts to cater for larger parts and different batch volumes.
SYNERGi (Sprint) Cell 2
Ayrshire Precision’s second SYNERGi cell was installed in September 2023.
This cell, incorporating the Puma 2100SY lathe, is similar to the first cell but instead features a 20kg payload industrial robot and a 900mm x 900mm table for processing smaller components.
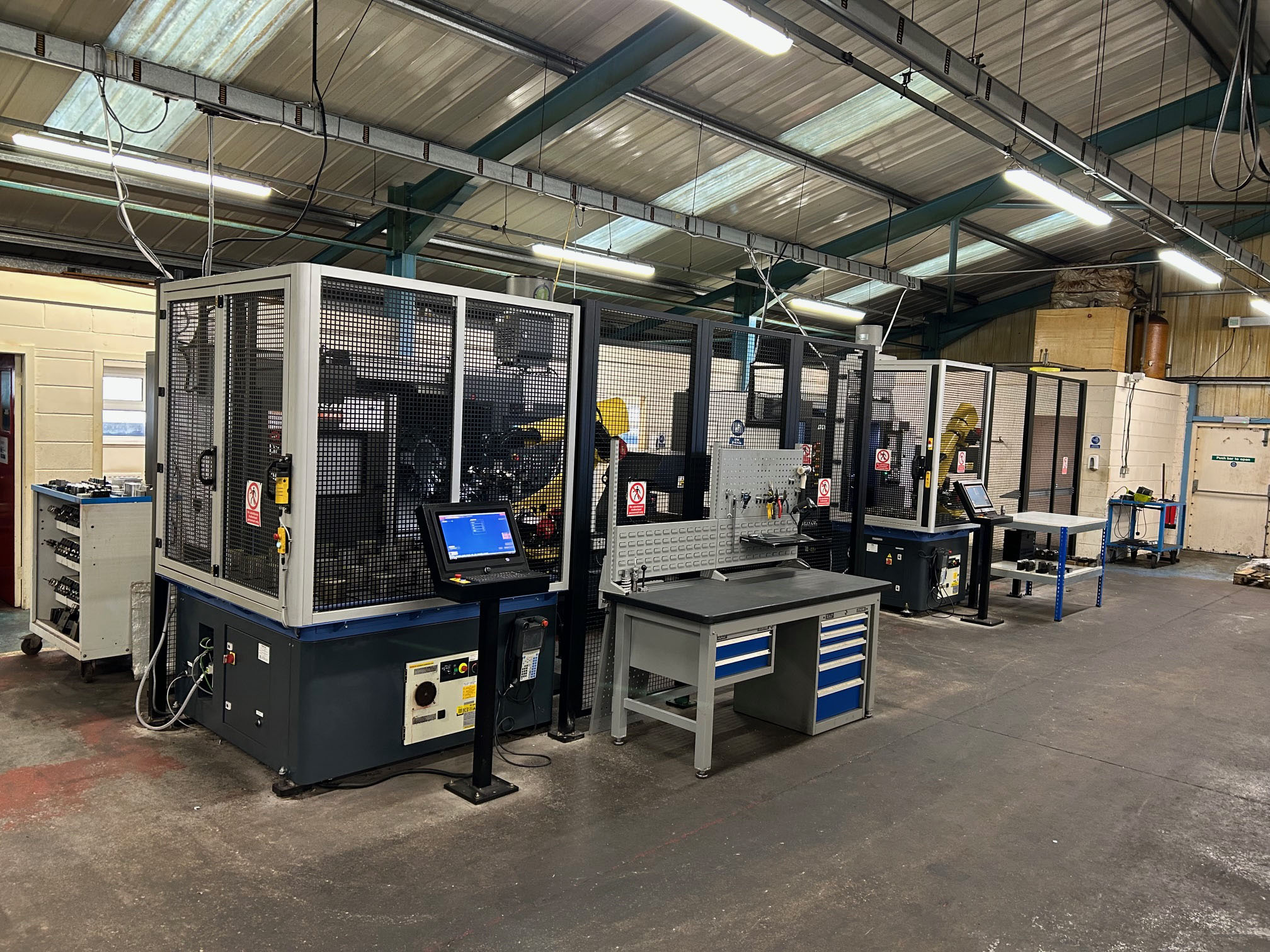
Cell operation
The automation process (for both cells) involves the robot picking up a workpiece from the table (grid plate) in a programmed sequence and, using the lathes’ auto door opening facility, loads the part into the machine’s main (left) spindle. The door closes to enable the machining of the part’s front end.
Once completed, the part is transferred (in-process) to the sub-spindle and the machining of the back end occurs.
After all machining operations are finished, the robot picks up the next sequenced workpiece from the table and, in one continuous movement, loads it into the main spindle and removes the finished part from the sub-spindle, returning it to its designated position on the table.
The process is then repeated until the entire batch has been machined.
“Every time the auto door opens, a completed part is removed from the sub-spindle and a new part is loaded into the main spindle. The process is fast, seamless and continuous.
“Furthermore, one member of staff is able to operate both cells simultaneously.”
Chris Hepburn, Managing Director at Ayrshire Precision
With less labour intervention required, Ayrshire Precision’s small part turning operation is now more efficient and profitable, and the creation of its two cells has also helped free-up a couple of its operators enabling them to be deployed to other areas of the machine shop – setting up and tending different machines etc.
“The investment in our two SYNERGi cells is paying dividends. We have two inherently flexible automated cells that, to a large extent, have not only helped us future-proof our small turned part operations, but have also increased our overall capacity too.
“Although, initially, there was some anxiety concerning our move towards automated production, the results have exceeded our expectations. Working in collaboration with Mills has enabled us to benefit from unmanned production and become more productive and profitable as a consequence.”
Chris Hepburn, Managing Director at Ayrshire Precision