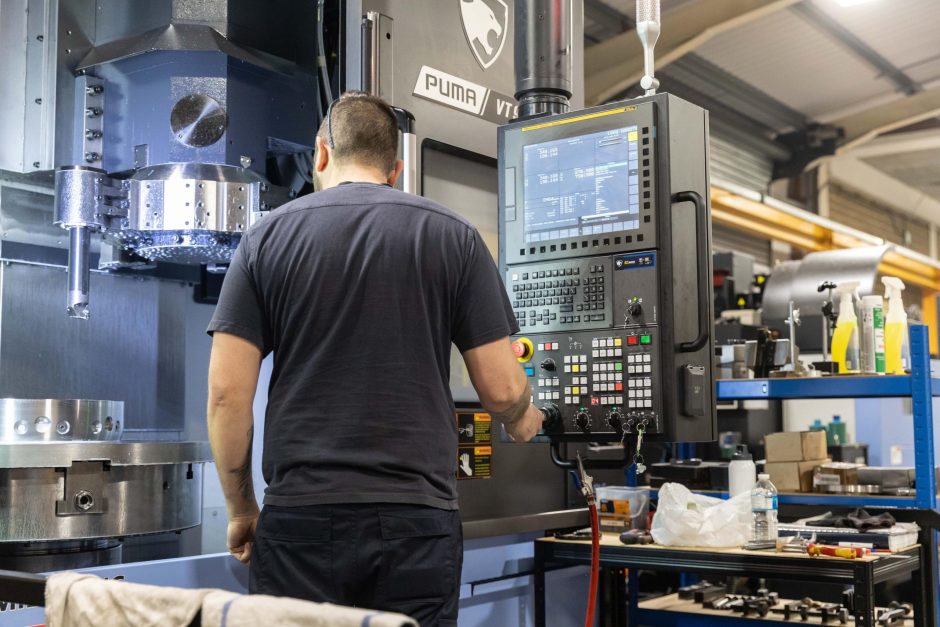
Leading precision subcontract specialist, Markyate Precision Machining (MPM), committed to continuous improvement, invests in 12 new, Fanuc-controlled Doosan and DN Solutions’ machine tools over the last seven years in order to increase its in-house machining capacity and capabilities, improve its productivity and process efficiencies, strengthen its supply chain position with existing customers and facilitate its entry into new market sectors.
Mills CNC, the exclusive distributor of DN Solutions’ and Zayer machine tools in the UK and Ireland, has recently supplied leading precision subcontract specialist – Markyate Precision Machining Co Ltd., with a new vertical turning lathe.
The machine, a DN Solutions’ 32” chuck Puma VT 900, was installed at the company’s 9000 sq. ft. facility in St. Albans, Hertfordshire in July 2023, and is being put through its paces machining a range of large, complex components, primarily for the oil and gas sector.
Made from hard and difficult-to-machine materials (i.e., Stainless Steels, Duplex etc.), these parts are machined in small batches to tight, tied-up geometric tolerances and exacting surface finish requirements.
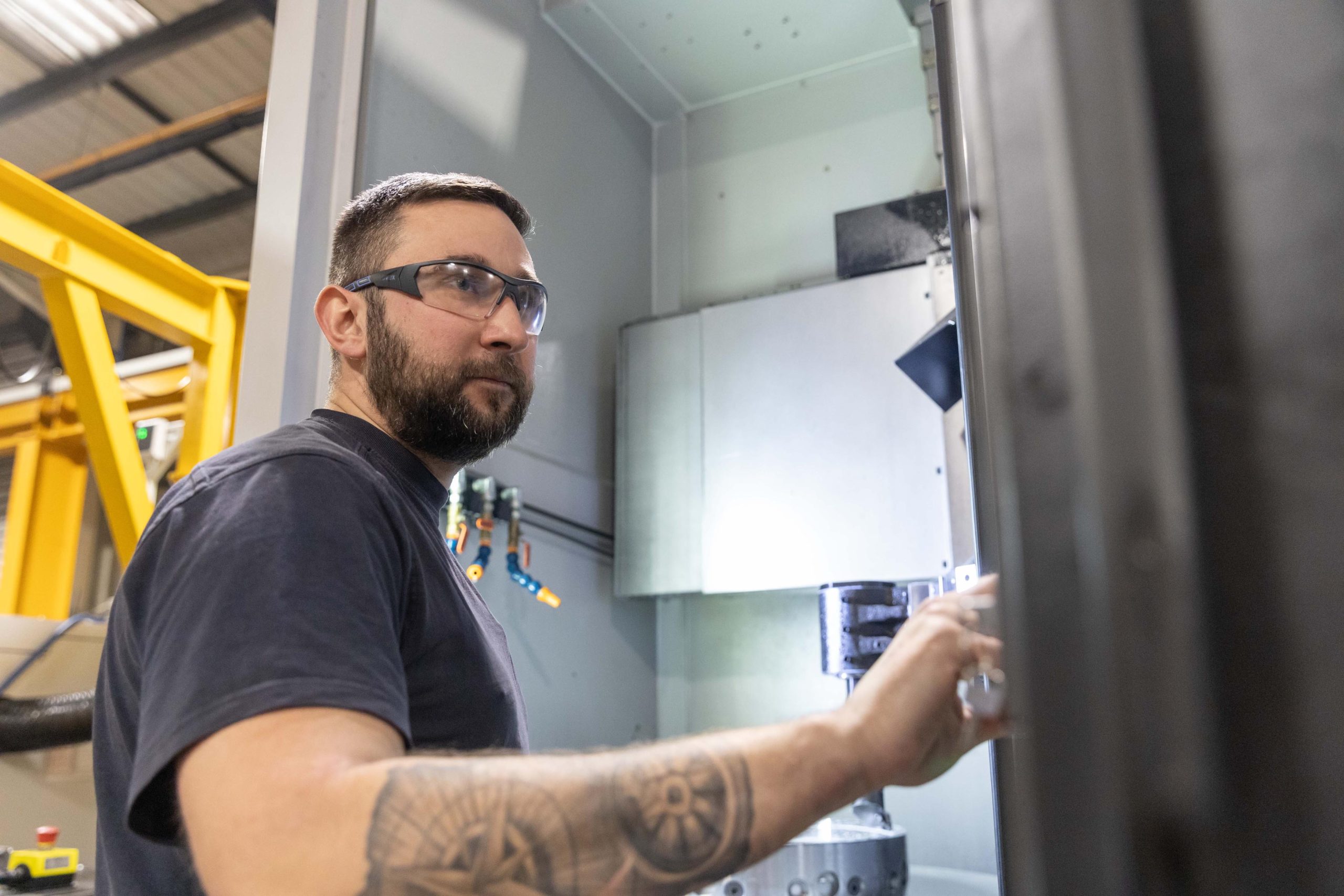
The investment in the VT 900 was made, primarily, to enable MPM to bring this type of large oil and gas work back in-house, and the decision helps illustrate and underscore the company’s future ambition to focus on high-precision machining of medium-to-large components for a range of industries and sectors.
“The VT 900 is a rigidly-designed and built box guideway vertical turning lathe with a 900mm maximum turning diameter and an 850mm maximum turning length/height.
“The machine’s large working envelope and its powerful, high-torque spindle (45kW/1,800rpm/4443N-m), make it ideal for the heavy-duty turning operations and the machining of large components, which we see as a high growth area for the business moving forwards.
“The VT 900 delivers power, speed, precision and machining flexibility and is also backed by Mills’ after-sales support services (i.e., machine tool servicing, operator and programmer training, spares and replacement parts etc.), which cannot be faulted, and which were also key factors in our decision making process.”
Dean Bygate, Operations Director at MPM
To help improve MPM’s productivity and process efficiencies, the machine was also supplied with through-spindle-coolant capability (70bar), a manual tool setter, an auto door facility and a Filtermist extraction unit.
Relationship with Mills CNC
The VT 900 might be the latest machine tool MPM has acquired from Mills CNC, but the relationship between both companies stretches back seven years to 2017, when the company invested in its first Doosan machines – a new, large-capacity Puma 400 lathe, a box guideway Puma GT 2600 lathe and a DNM 4500 (3-axis) vertical machining centre.
Since then, more investments have followed, frequently and regularly.
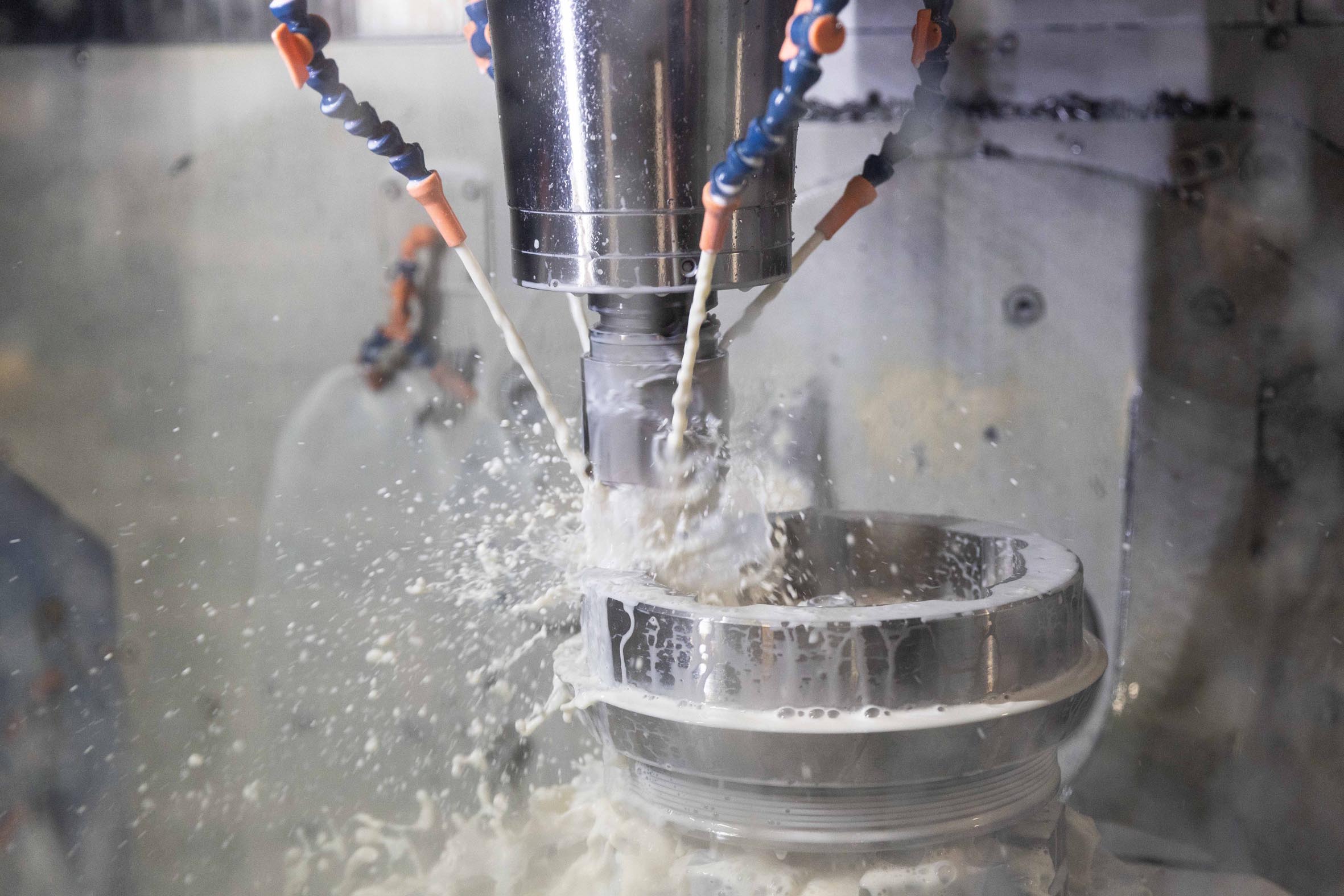
To upgrade and help strengthen its small turned part processing operation, MPM invested in two Lynx 2100B lathes with bar feeders in 2020 and, a year later, to help meet a significant increase in demand from an existing customer, seven more (Doosan) machines were acquired.
This latest haul included two new DVF 5000 simultaneous 5-axis machines which have helped MPM achieve improved process efficiencies by reducing the number of machining operations (from two down to one) required to produce high-precision components that, once machined, surface treated and painted, are then assembled to create high-strength, anti-corrosion undersea housings and enclosures.
“Demand from our international submarine customer really took off in 2020/ 2021.
“Prior to then we were making and supplying 18 completed assemblies a week, but this increased dramatically in 2021, requiring us to supply 54 completed assemblies a week: a 200% increase!
“It was a tall order, and it soon became clear that to meet our customer’s new expectations we needed to significantly increase our in-house machining capacity and capabilities – fast.”
Dean Bygate, Operations Director at MPM
MPM approached Mills to discuss how best to increase and upgrade its existing machine shop capabilities and this resulted in the company placing orders for seven new machines that, in addition to the two new DVF 5000 machining centres mentioned above, also included three new lathes – a Puma 4100, a Puma GT 3100 and a Lynx 2100B (with a bar feeder), and two new DNM 4500 machining centres.
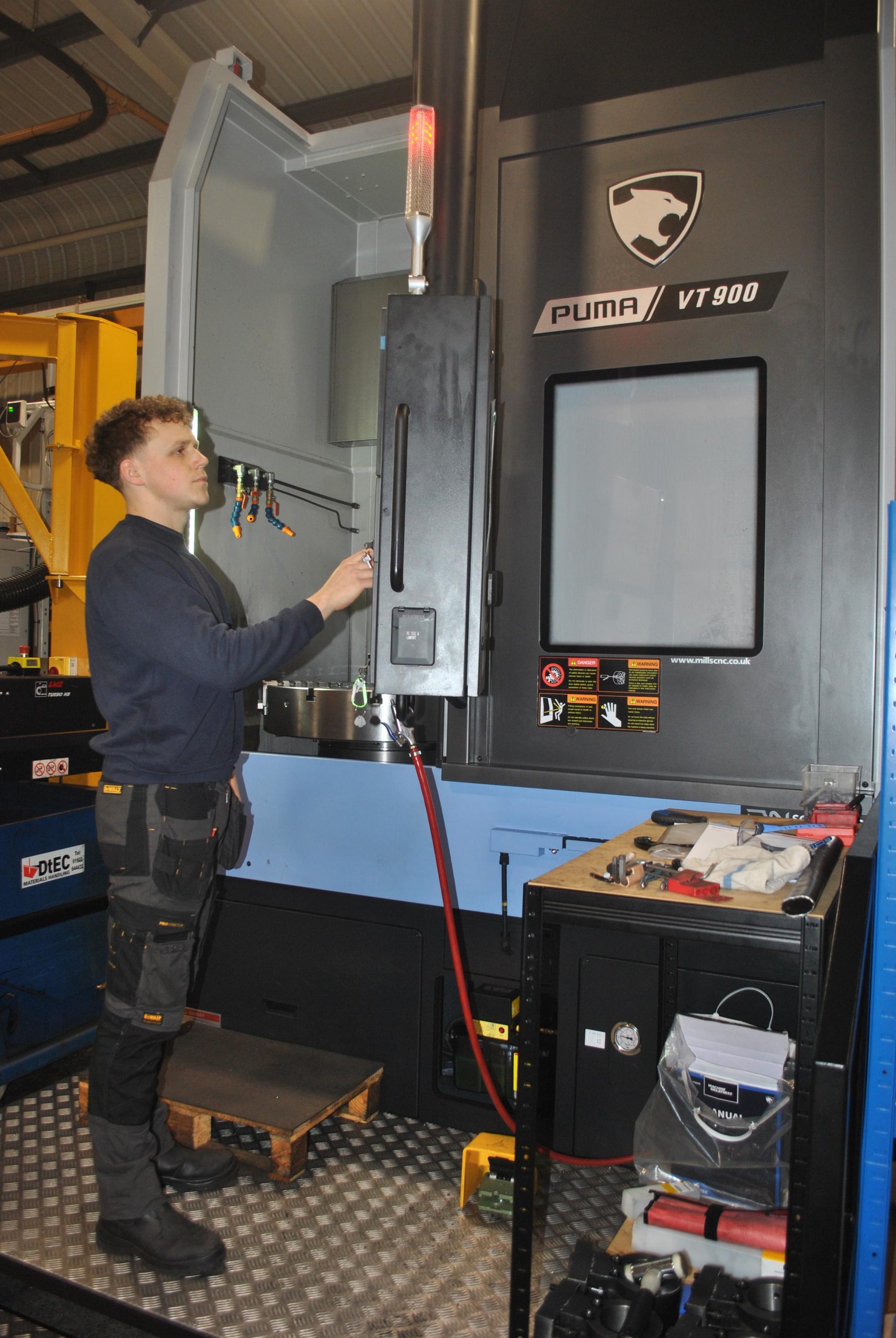
“Doosan machines are reliable and deliver excellent cutting performance. They help us achieve and maintain quality, and ensure that we can hit customers’ (often stringent) delivery schedules.
“Furthermore, owing to Mills’ stocking policy, machines are often readily available. This is a particular strength that Mills has over many other machine tool suppliers, and is another reason why they are our ‘first port of call.’
Dean Bygate, Operations Director at MPM
Markyate Precision Machining (MPM): a closer look
MPM is a family-owned business that was first established in the 1950s.
The company has a rich pedigree and a reputation based on innovation, engineering excellence, continuous improvement and customer service.
Currently employing 24 members of staff (19 in production-based operations), the company regularly invests in its people, in its plant and equipment and in its processes and systems.
The company runs a successful Apprenticeship Programme in conjunction with Milton Keynes College which has helped MPM considerably reduce its age profile and address potential skills shortage issues that could affect growth and performance in the future.
MPM has, in recent years, also introduced a sophisticated MRP/ERP system to improve operational and process efficiencies and, to improve part inspection, has invested in a portable Keyence benchtop CMM.
MPM operates across a number of sectors and industries (aerospace, medical, marine, oil and gas, specialist machine tool builders etc.).
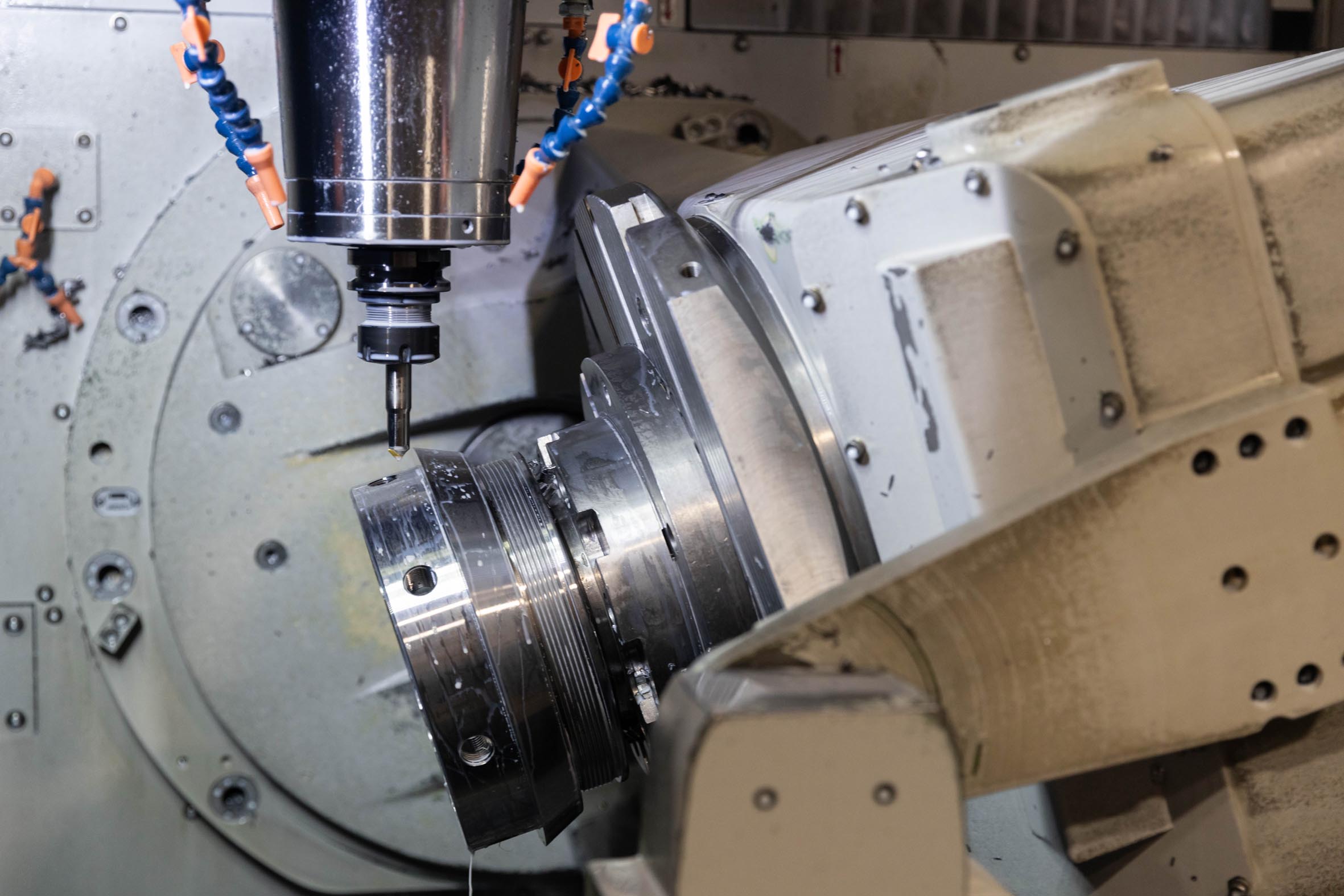
In addition to machining high-quality components, the company also designs and manufactures advanced tooling systems and solutions for customers, as well as for its own use.
As well as CNC machining, MPM specialisms include turnkey projects, technical consultancy (including Design for Manufacture), assemblies and sub-assemblies, materials science and materials’ machinability.
“We are not your typical machine shop and can provide customers with a range of high-quality and integrated manufacturing services and specialisms.
“From prototyping and one-offs, through to small-to-medium batch processing, MPM has the knowledge, experience and technology in place to help customers make things better.
“Our investments in Doosan and, more recently, DN Solutions’ machine tools, and the strong relationship we have built with Mills CNC, have made us more efficient, productive and competitive too.”
Dean Bygate, Operations Director at MPM