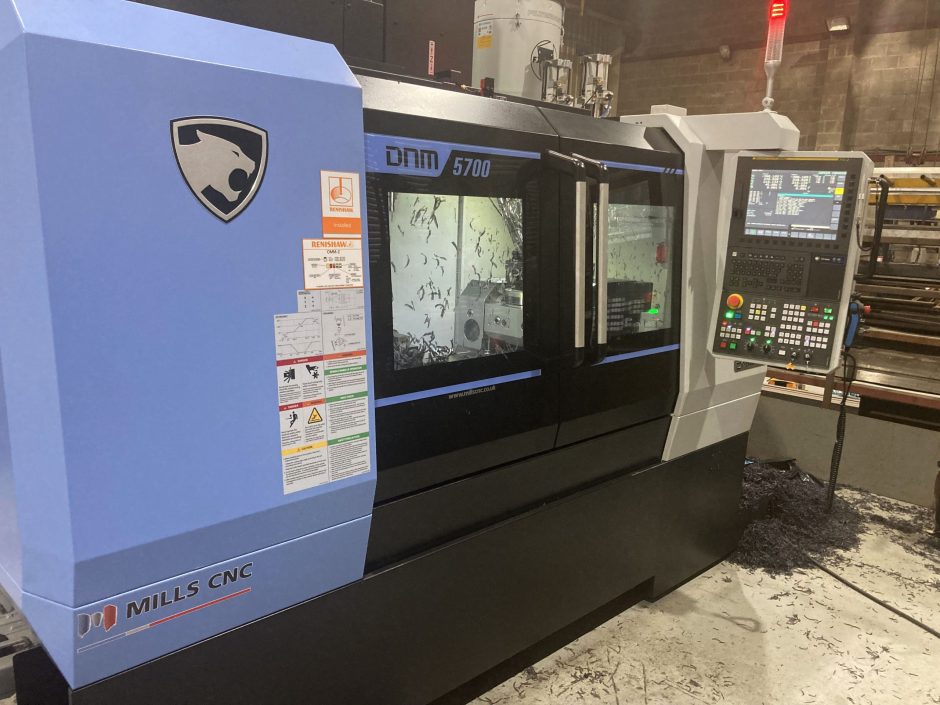
New engineering business start-up invests in a new, high-performance DN Solutions’ vertical machining centre from Mills CNC.
Mills CNC, the exclusive distributor of DN Solutions’ and Zayer machine tools in the UK and Ireland, has recently supplied Custom Metalworks Ltd., a new precision engineering specialist start-up providing high-precision CNC machining, customised fabrication and welding, and CAD/CAM consultancy services, with a new DN Solutions’ (4th-Generation) DNM 5700 vertical machining centre.
The new machine, installed at the company’s machine shop facility in Ormskirk, Lancashire in June 2024, is powerful, fast and accurate. It is equipped with the latest advanced Fanuc i Plus control with a 15” touchscreen iHMI, and features an 18.5kW/12,000rpm directly-coupled, high torque spindle (117.8N-m), a 1050mm x 570mm worktable (with a 1000kg maximum table load) and a 30-tool position ATC.
The machine, supplied to Custom Metalworks as part of the investment package, was also delivered with a Deltron GFA-200EH (5-axis) rotary table, Renishaw tool and table probing systems and a FilterMist extraction unit.
The DNM 5700 in action
Since being installed, the DNM 5700 has been put through its paces machining a range of performance-critical plastic components for a leading manufacturer of innovative patient positioning products and equipment (i.e., support frames, sets, extensions, systems and attachments etc.), designed for a range of surgical procedures where the patient lies prone on an operating table.
Custom Metalworks machines parts and sub-assemblies for this customer’s best-selling spine frame systems which, essentially, are versatile, cost-effective table-top platforms, positioned underneath the patient, that can be easily fitted to any standard operating table, and that enables patients to be safely and securely positioned/re-positioned during spinal operations and procedures.
Spine frames are fully radiolucent, and feature spine, hip and chest supports that can be easily adjusted to accommodate different patients’ height, weight, body-types etc.
These supports, made from Nylon 6, are fixed to each frame system’s (parallel) rails by clip locks with a quick-release function.
“Nylon 6 is a durable and reliable engineering plastic with high mechanical resistance that exhibits good machinability characteristics and sliding properties.
“The Nylon parts we machine are accurate and require a good surface finish, but geometric tolerances are not that exacting. We machine the parts using coolant, as opposed to adopting ‘dry’ machining methods, in order to control heat build-up, protect tool life and optimise chip evacuation from the cutting zone.
“The key manufacturing issues for us machining these parts concern component repeatability’s, security of supply, lead time fulfilment and cost.”
Jack Eckersley, Owner and Managing Director at Custom Metalworks
Custom Metalworks machines and supplies batches of supports, which comprise brackets, clips, modular sides etc., to the customer.
Batch sizes vary depending on the support itself and the customer’s order requirements, but can be up to 200-off per month for certain products, and less for others.
Part cycle times are typically around 30 minutes allowing Jack to focus on other activities i.e., fabrication and welding, design consultancy projects, admin etc., whilst the machine is running.
In addition to Nylon 6, Custom Metalworks has also machined stainless steel and aluminium components and fixtures on the new machine.
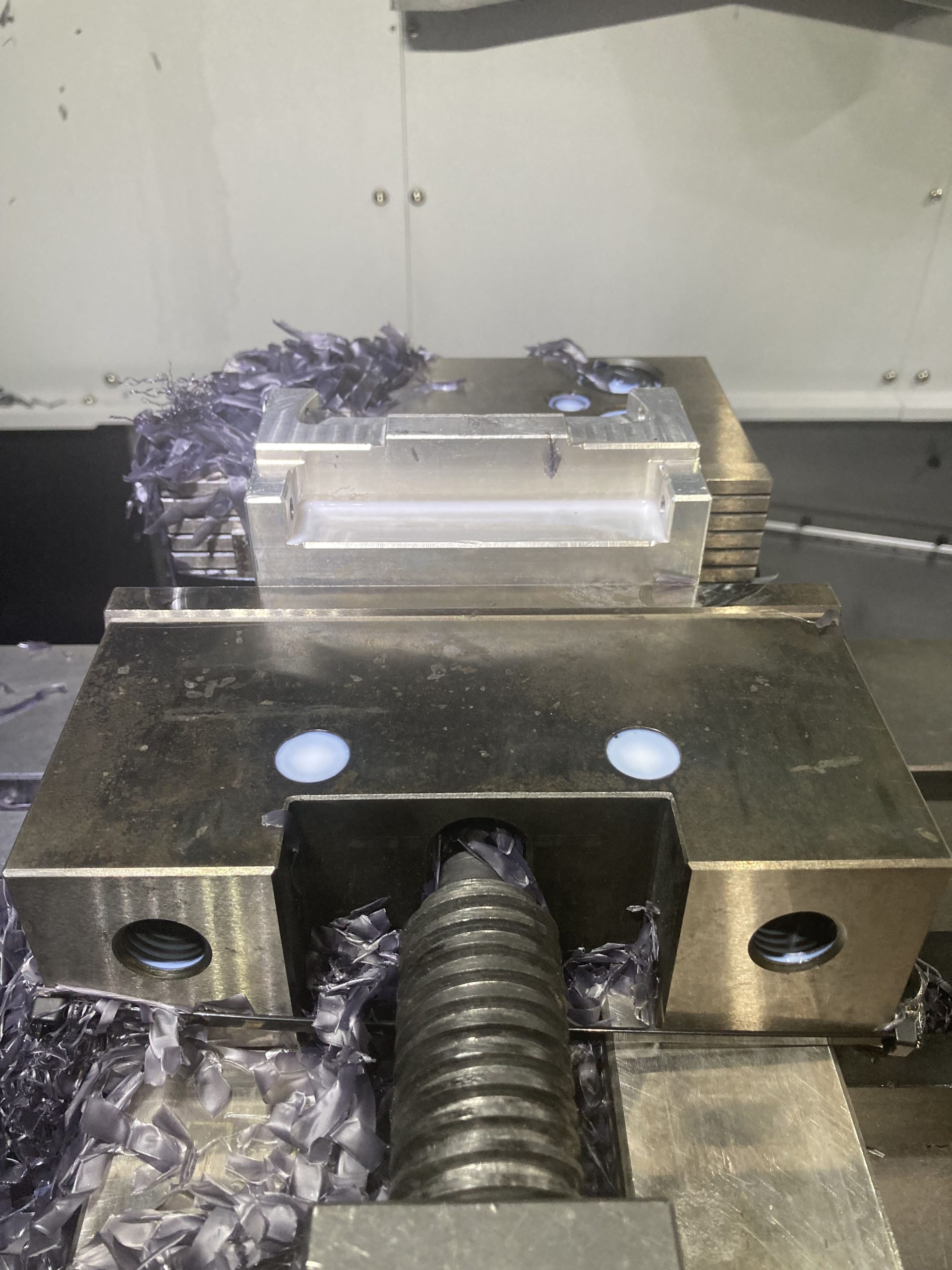
About Custom Metalworks
Custom Metalworks was established in 2023 by owner and director, Jack Eckersley, an apprentice trained, time served and entrepreneurial engineer.
Jack started his engineering career at a leading design and manufacturer of innovative, high-quality products and solutions for the glass container manufacturing industry.
Having completed his 4-year apprenticeship at the company, plus an additional period of time on the machine shop floor working as a manufacturing engineer, Jack made the decision to leave and start up his own precision engineering subcontract business – providing specialist high-quality CNC machining and fabrication and welding services to customers.
“It’s something I always wanted to do. I was confident that my toolmaking background combined with experience in CAD/CAM, CNC milling, inspection, reverse engineering and design for manufacturing would stand me in good stead and ensure that the new venture would be a success.”
Jack Eckersley, Owner and Managing Director at Custom Metalworks
At around the same time as setting up the new company, Jack was presented with an opportunity that ultimately shaped the direction of travel for his fledgling business.
Opportunity knocks
“I was introduced to a local medical equipment company that specialised in the design and manufacture of innovative patient positioning products.
“The company had, for a variety of reasons, recently decided to bring its manufacturing operations in-house and had (already) invested in a number of CNC machine tools (including a simultaneous 5-axis machining centre), but needed help in setting up and organising its machine shop, and in developing secure and efficient programs and processes to machine components for its product ranges.”
Jack Eckersley, Owner and Managing Director at Custom Metalworks
Jack took the decision, monumental as it transpired, to join the company, working during the day in its machine shop whilst focusing on his new business venture in the evenings and at the weekends.
This arrangement enabled Jack to build good working relationships with the customer, acquire a thorough understanding of its product ranges and, seeing as he had developed many of them, know its manufacturing methods and processes…inside-out.
However, after a few months, instead of ‘burning the candle at both ends’, trying to run the customer’s machine shop whilst, at the same time, getting his own business off the ground – a mutually beneficial decision was made to transfer all of the customer’s machining operations over to Custom Metalworks.
“We, in effect, became the customer’s de facto machine shop. But, to cope with this new influx of work, we needed to increase our machining capacity and capabilities…fast.
“From a cost and capability perspective, I made the decision NOT to replicate what was already in place at the customer’s machine shop, preferring, instead, to purchase a smaller, high-performance and more flexible 3-axis machining centre with large working envelope and a 5th-axis rotary table with hydraulic clamping capabilities for 3 + 2 and 4 + 1 machining of specific parts and fixtures.”
Jack Eckersley, Owner and Managing Director at Custom Metalworks
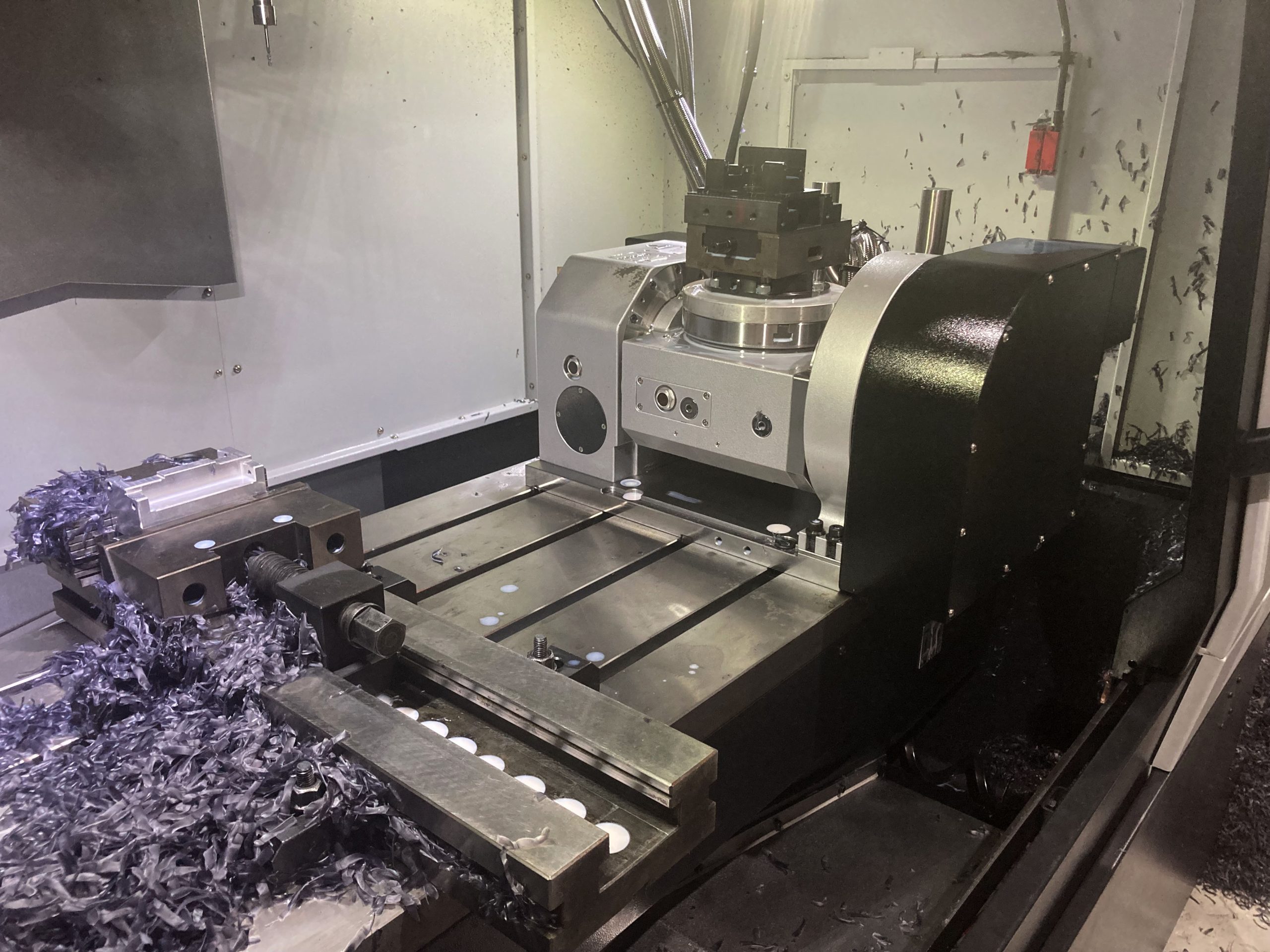
The DNM 5700 investment decision
Jack did his homework and narrowed down his search for potential machine tool suppliers.
Having already had experience of Doosan machines and Mills CNC from his time at the glass container manufacturing company, he approached Mills to find out more about the company’s 3-axis milling ranges, and was introduced to popular and proven DNM series.
This ultimately culminated in a visit to Mills’ stand at MACH 2024 where he saw the new (4th-generation) DN Solutions’ DNM 5700 in action.
“I was looking for a machine that delivered fast processing speeds, high accuracies and good surface finishes, and that would enable us to machine large and/or smaller multiple parts in a single set up.
“The DNM 5700, with its advanced spindle technology, rigid and thermally-stable build, fast rapids and large working envelope seemed to offer the ideal solution.
“Having talked to Mills, I placed the order there and then at the Show. Since being installed in June 2024, the DNM 5700, following on-site training, has been in full operation ever since.”
Jack Eckersley, Owner and Managing Director at Custom Metalworks
Future
Custom Metalworks offers something unique to the market and its customers – high-quality machining, customised fabrication and welding services, design for manufacturing consultancy etc.
The investment in the DNM 5700 has improved the company’s machining capacity, capabilities and flexibility. Although Jack is working long hours, the DNM 5700 is coping well with the demands placed upon it.
As far as the future is concerned, Custom Metalworks (never a company to rest on its laurels), is looking at the potential of streamlining its machining operations by investing in automation (i.e., robot handling system) to further increase productivity and improve process efficiencies.