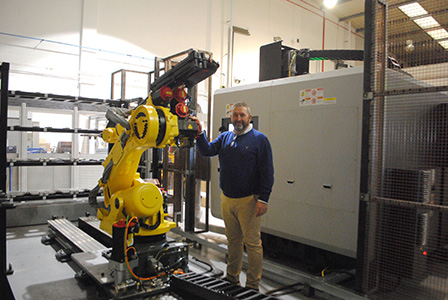
A Mills CNC custom-designed and built automated manufacturing cell is being installed at Lenane Precision’s facility in Smithstown, Shannon, County Clare in March 2020.
The cell represents a significant investment for Lenane and, when operational, will run 24/7 delivering significant productivity gains and process efficiency improvements to the company…substantially increasing its competitiveness.
This article describes Lenane’s automated cell in more detail, and the rationale underpinning the investment.
The cell comprising two Siemens 840D-controlled Doosan DVF 5000 (5-axis) machines and a Fanuc industrial robot also features:
- A robot positioning track (also known as a RTU – Robot Transfer Unit) that runs between the two adjacent positioned DVF 5000 machines enabling the robot to service both (i.e. undertaking part loading and unloading operations).
- Integrated racking systems that hold up to 36 x standardised sized pallets (400mm x 400mm with up to 140kg maximum load) onto which workpieces are clamped and then loaded into the DVF 5000 machines, and machined components are unloaded from the machine and stored.
- 2 metre high safety caging/fencing that encloses the robot track and that restricts access to the DVF 5000 machines’ loading/unloading operations.
At the heart of the system is a sophisticated and powerful touchscreen HMI that uses Mills’ proprietary SYNERGi software to control the cell and that provides a seamless interface with the cell’s machine tools, robot etc.
Background
Since 2012 the company has, almost exclusively, become a Doosan machine tool user. In the last eight years Lenane has purchased four new Doosan machining centres, including two 5-axis machines, and three new multi-tasking lathes from Mills CNC.
Over a similar period of time the company has metamorphosed from a toolmaking company to one of Ireland’s premier precision subcontractors.
Lenane serves a number sectors – aerospace, medical devices, oil and gas etc., and it is the company’s growing aerospace business (specifically the machining of high-precision aero-structure parts), and its desire to move up and strengthen its position in the aerospace supply chain, that was the driving force behind the automated cell’s inception.
Explains Jim Lenane, Managing Director:
“The aerospace sector is global, challenging and demanding and, whilst success is never guaranteed, if you unable to meet the Industry’s exacting quality requirements, stringent lead-times and cost down demands you’re on a hiding to nothing”.
A quick look at some of Lenane’s recent business decisions and activities demonstrate the company’s commitment to growing its aerospace business:
- The company has achieved AS 9100 certification and is a SC21 member;
- The company is an active participant of the Emerald Aero Group (an Irish manufacturing consortia established to support the aerospace sector’s supply chain;
- The company has invested in advanced Doosan 5-axis machine tool technologies.
Cell rationale
Lenane’s recent multi-axis, multi-tasking machine tool investments demonstrate its commitment to one-hit machining. For some companies the performance improvements gained from such investments may have been enough – but not for Jim Lenane.
“Continuous improvement is a journey not a destination”, he explains.
“My vision and ambition has always been to exploit the true potential of automation – the objective being to achieve continuous and seamless production in our facility, and to reduce (as far as is possible) the labour component from our machining processes.
“In reality I was waiting for the right time to realise the vision and, at the tail end of 2018 with orders from our existing aerospace customers reaching an all time high and with firm commitments from them to place more orders with us in the future – the decision to put these plans into action was made.”
Cell imperative
From the outset a number of potential automation routes were discounted by Lenane. These included investing in machine tools with integrated automatic pallet changers.
Explains Jim Lenane:
“Integrated workpiece pallet changers were clearly an option for us but, from a continuous production perspective, this route (i.e the number of pallets available), had its limitations. I wanted something more ambitious – an automation solution that was future-proof.
“I knew that an automation solution that involved industrial robots was the direction of travel – so we set about exploring the options and alternatives.”
To help the company select the optimum solution a number of prerequisites were drawn up.
Cell imperatives
- Flexibility:
Lenane’s manufacturing cell needed to be inherently flexible.
Although the company had earmarked the cell for machining high-precision aerospace components these parts would not be identical and would differ in their dimensions, materials, batch size requirements etc.
The intention was, in the first instance, to create a cell comprising two 5-axis machines serviced by one industrial robot. However, it was important that, in the future and to improve productivity still further, that additional machine tools could be integrated into the cell system if and when required.
- Compact:
Owing to floorspace constraints at Lenane’s facility the cell needed to be compact and have a linear configuration.
The idea of positioning two machines adjacent to each other and have the robot service them from behind on a track would optimise the space available.
- Single source:
An automated cell comprises, quite literally, a number of moving parts. Lenane’s intention was to opt for a one supplier to project manage the cell’s design, development and implementation – including the sourcing of all cell elements and equipment, and to manage all relationships with third party suppliers.
Comments Jim Lenane:
“We were looking for a turnkey solutions supplier to manage all aspects of the cell’s design and build. From an efficiency (and sanity) perspective it was important that we had a single point of contact for all communications relating to the cell and not have to manage relationships with the different equipment suppliers.”
Lenane approached a number of turnkey providers early in 2019 with their requirements and ultimately awarded the project to Mills CNC.
Why Mills CNC?
Every year Mills CNC manages a number of turnkey projects for new and existing customers. A significant percentage of these involve industrial robots and the creation of flexible automated manufacturing cells.
Says Jim Lenane:
“We already had a good relationship with Mills CNC. We know them and they know us – so there isn’t a learning curve involved as there would be if we had selected a new (and untested) supplier.
“We have invested heavily in Doosan machines over the years and, we believe, that their performance and reliability is second to none. We also consider the after-sales service and support provided by Mills CNC is the ‘best in the business’.”
The Doosan DVF 5000 machines
The machines, providing full 5-axis simultaneous machining capability, are equipped with 17.5kW/12,000rpm spindles and servo-driven automatic tool changers (120 position), and feature linear guides and integrated thermal compensation systems for increased accuracies and repeatability’s.
The two machines specified by Lenane were both equipped with the Siemens 840D control.
DVF 5000 machines are automation ready and can be supplied with a automatic door open/door close facility. The machines also have good (side) access for robot loading and unloading.
Says Jim Lenane:
“The DVF 5000 machines’ speed and accuracy look impressive. The 120-position tool changers on both machines will help us ensure 24/7 unattended and lights-out operations, as will their high-efficiency swarf management systems. And the integration of spindle and table probing for in-process inspection ensures greater process security and reliability.
“Although the machines are an integral part of the cell – they can, if required, be used independently and autonomously – thereby increasing our overall machining flexibility.”
Summary
Lenane’s flexible automated manufacturing cell is being delivered in March 2020, with on-site training occurring later in the month.
The cell, the first of its kind in Ireland, represents a completely bespoke automation solution and, needless to say, anticipation and expectation amongst Lenane’s 25 members of staff is high.
Concludes Jim Lenane:
“A complex turnkey solution of this kind takes time to design and develop, and Mills CNC have pulled out all the stops to deliver something that is truly special.
“Our cell will soon be installed at our facility and we can’t wait to put it through its paces.”