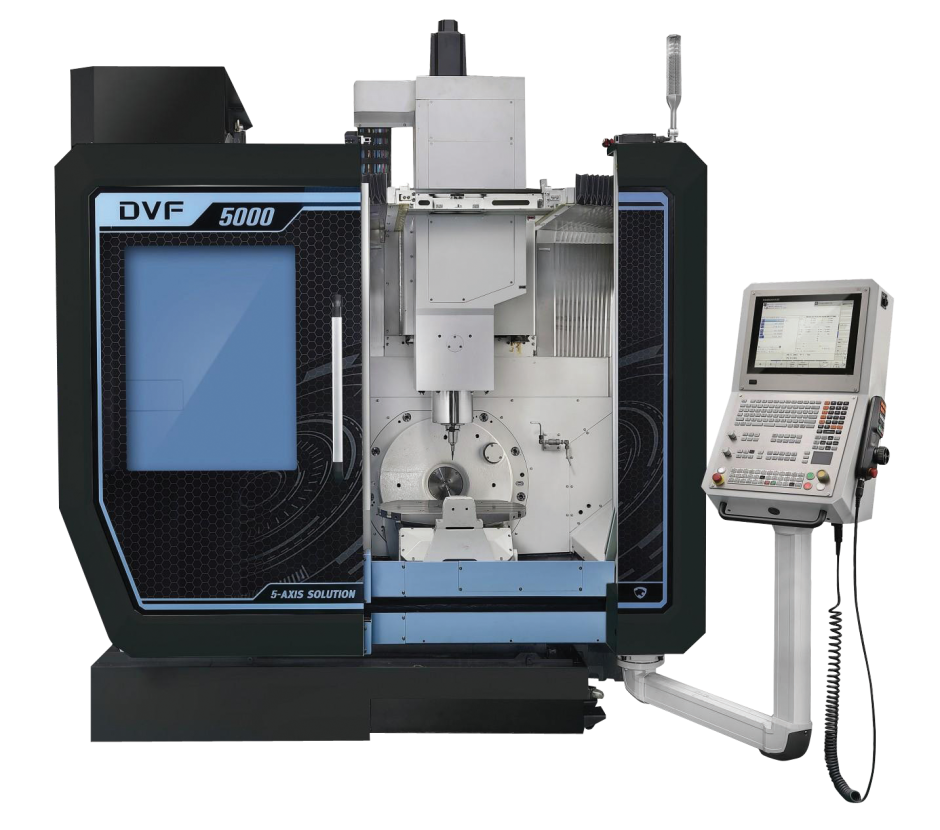
Mills CNC introduces new, second-generation DN Solutions’ DVF 5000 simultaneous 5-axis machining centres into the UK and Irish markets.
Available from Mills CNC from May 2025 onwards, the new series, building on the popularity and success of its predecessor, delivers improved accuracies, faster processing speeds and greater machining flexibility – taking one-hit machining to a whole new level.
Mills CNC, the exclusive distributor of DN Solutions’ and Zayer machine tools in the UK and Ireland, has introduced an advanced range of simultaneous 5-axis machining centres into the market.
The second-generation DVF 5000 series, successor to the earlier DVF 5000 range first introduced back in 2018, has raised the bar for ‘one-hit’ machining and, building on the popularity and success of its predecessor, delivers improved accuracies, faster processing speeds and greater machining flexibility.
“If you’re going to launch a new, next-generation range of machine tools into the market, you need to make sure that it’s significantly better than its predecessor; especially if that predecessor was the most popular, best-selling simultaneous 5-axis machining centre series on the market!
“But ‘hats-off’ to DN Solutions, because that’s exactly what they’ve achieved with their second-generation DVF 5000 machining centre range.”
Tony Dale, Group CEO at Mills CNC
The differences – the improvements:
Processing speeds
The new range of machines get down to business fast.
Faster X-, Y-and X-axis rapids (42m/min) and acceleration/deceleration rates (0.4g), combined with increased B- and C-axis rotation speeds (25rpm) and impressive Tool-to-Tool changeover times (1.3 seconds), deliver significant productivity gains – reducing part cycle times and work throughput.
The productivity improvements continue with the new series’ advanced spindle technologies too.
Standard second-generation machines are equipped with a directly-coupled 18.5kW/15,000rpm spindle – capable of processing a diverse range of materials in double-quick time. To increase machining capabilities, a built-in high-torque 30kW/15,000rpm/230N-m or a 37kW/20,000rpm high-speed option are available.
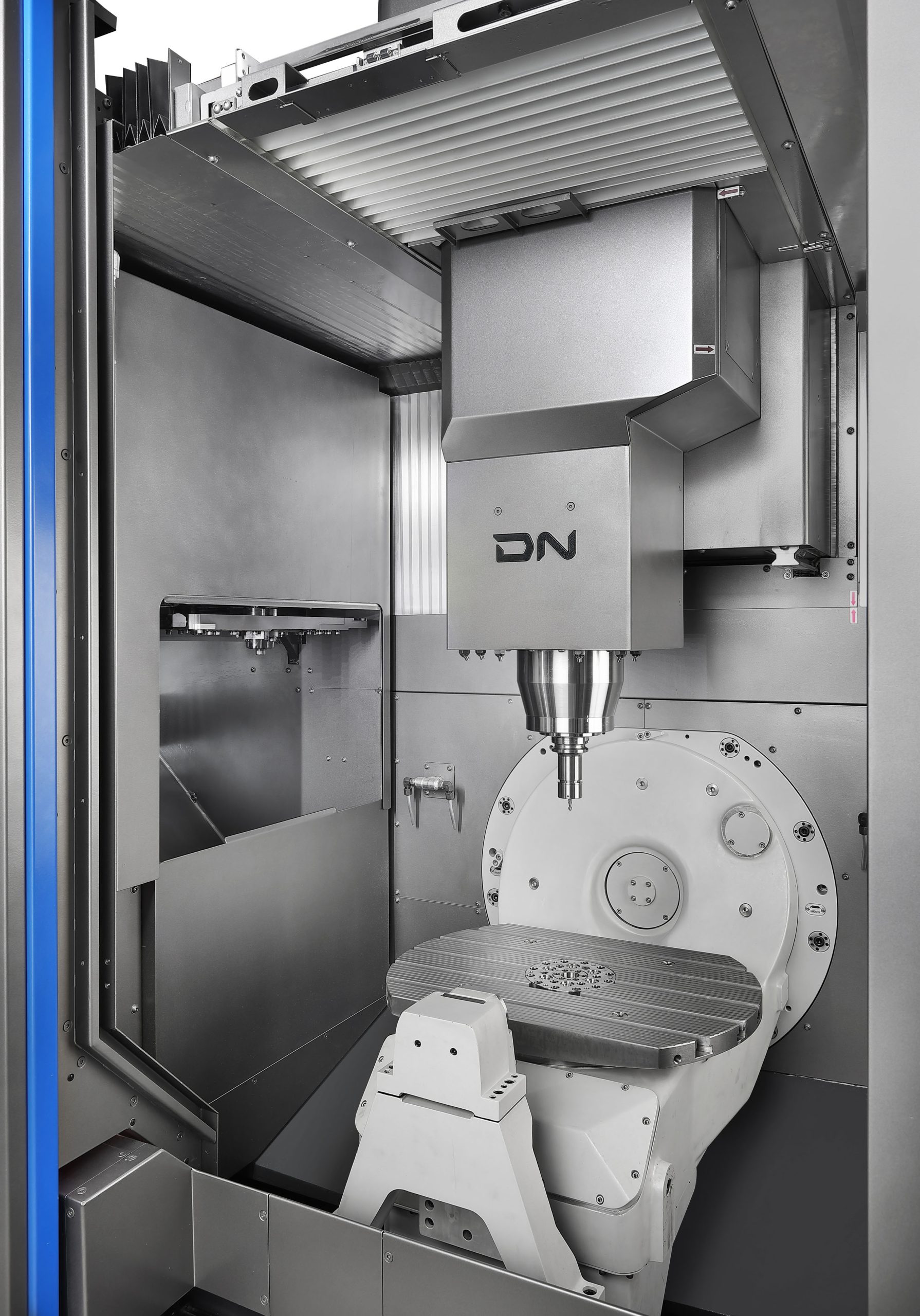
Accuracy and precision
Irrespective of the spindle type selected, all options feature advanced oil-cooling which, working in conjunction with strategically located sensors on/in the machines’ spindle head, column and bed, monitor thermal displacement throughout the machining process, automatically adjusting parameters to minimise the effects of thermal expansion and drift.
The incorporation of precision roller-type LM guideways and high-accuracy 0.0001 degree B- and C-axis rotational mechanisms, with the optional IKC (Intelligent Kinematic Compensation) system to monitor and adjust rotary axis errors, guarantees precision even over extended use and lengthy machining runs.
Flexibility and versatility
DVF 5000 second-generation machines can handle larger workpieces than their predecessors, and feature 630mm diameter rotary-tilting tables that can accommodate workpieces up to 600mm in diameter and 500mm in height.
With a 26% increase in table size, and an equally impressive 32% increase in the machining envelope available and a 20% increase in X-, Y- and Z-axis travels, customers can be assured that they will never be ‘pushed for space’ with the new machines.
Automation ready
The larger work envelopes and extended travels enables the seamless integration of automated work load/unload systems.
These can include DN Solutions’ tried and trusted compact AWC (Automatic Workpiece Changer) easy-to-install automated systems to facilitate 24/7 unmanned and unattended operations.
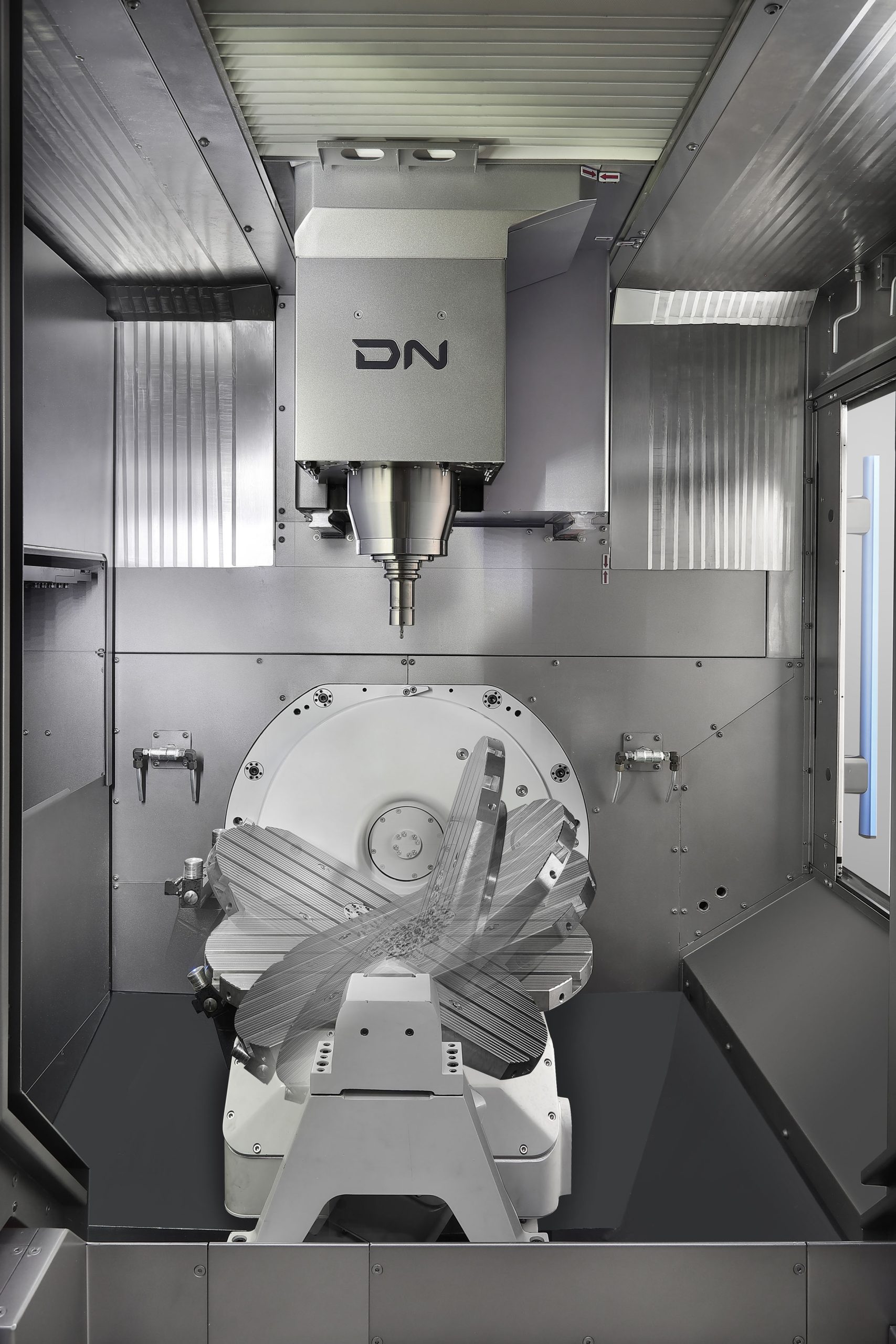
Operator use and convenience
The DVF 5000 Second Generation machines van be supplied with Fanuc, Siemens or Heidenhain CNC control systems – each boasting accelerated data and PLC (Programmable Logic Controller) processing speeds designed to speed-up everything from programming and program verification through to job setup and actual machining.
The Fanuc control option includes a collision prevention system (CPS), which actively monitors axis feeds, spindle dynamics and the workpiece, in real-time, to avoid collisions, damage and downtime.
The machines also feature a ‘re-located’ front-positioned tool magazine window that helps improve tool set-up operations, and a reduced distance between the operator and work table simplifies job setups.
Other improvements include six flood coolant nozzles (on the spindle’s front) to control heat build-up and chip removal, and a flushing nozzle on the machines’ beds to minimise chip accumulation.
As is standard with new DN Solutions’ machines, DVF 5000 second-generation machines feature a grease lubrication system that reduces oil consumption and ensures more eco-friendly machining centres.